We're driving
the digital
revolution
We provide superior quality solutions, keeping the focus on helping our customers reach their business goals.
Bring your breakthrough ideas to life with our full cycle development services
We are dynamic, multi-skilled team and can handle complete end-to- end software development services.
At Montbleu, we help to re-imagine business processes and build innovative digital products for an impeccable customer experience and faster time to market. Consulting-led approach on product strategy, shifting the paradigm from R&D intensity to R&D efficiency helps launch right products to the right market at shortest time to market right from advisory to design, implementation, and launch.
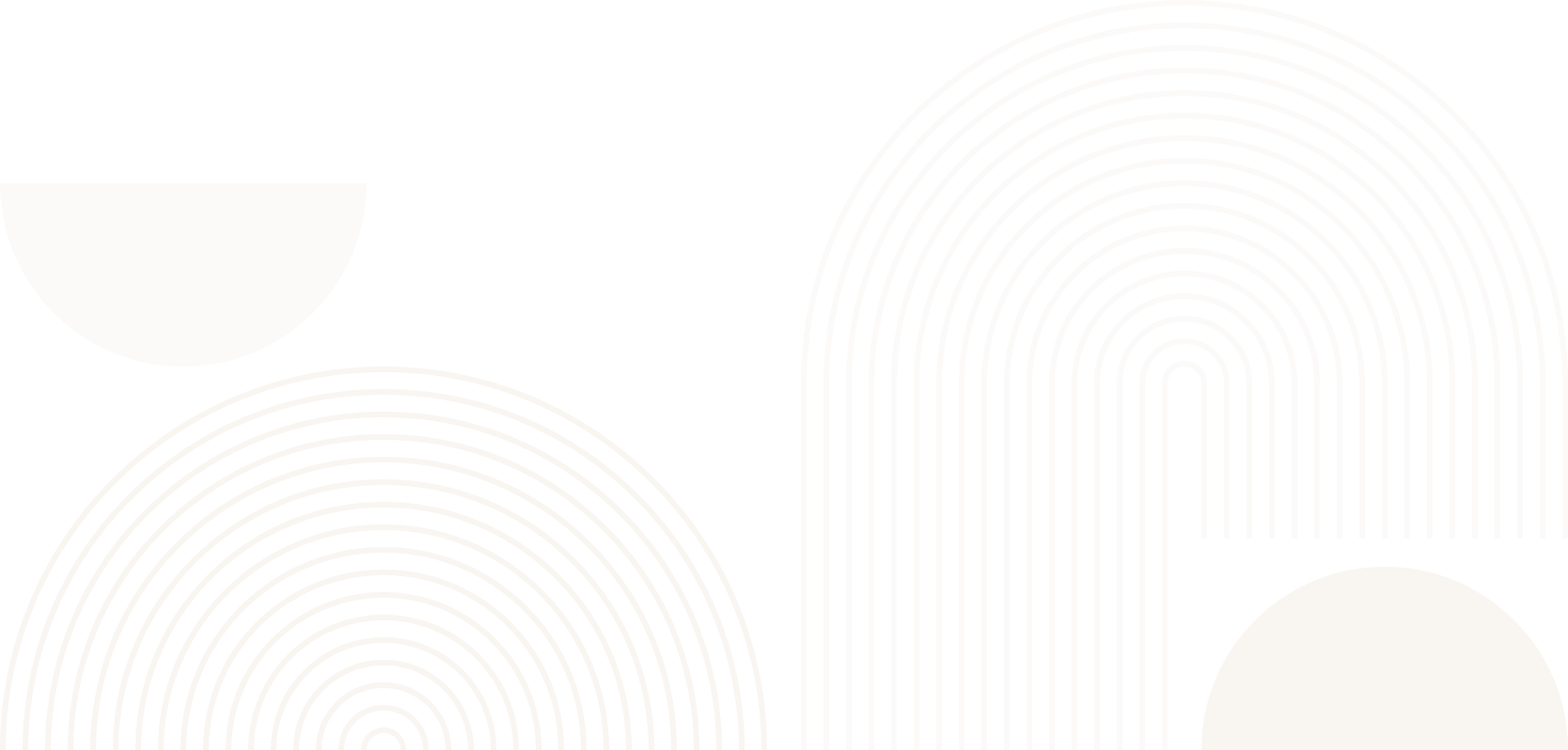
Knowledge Based Engineering
Engineering Enterprise Enablement – Automation & Technology
Automated framework for higher productivity, knowledge retention, and improved design process
Engineering Analytics – Improve operational efficiency, optimize development life cycle and improve time to market.
Cost Efficiency
Identification of inefficient processes; benchmarking of SG&A costs compared to industry peers/best practices; assessment and quantification of improvement effects; support with implementation.
Business Process Transformation
Project governance, clear reporting and meeting structures and operational support to implement transformation programs and adapt the organization during execution while ensuring full transparency and aligned communication.
Digital Services / Capabilities
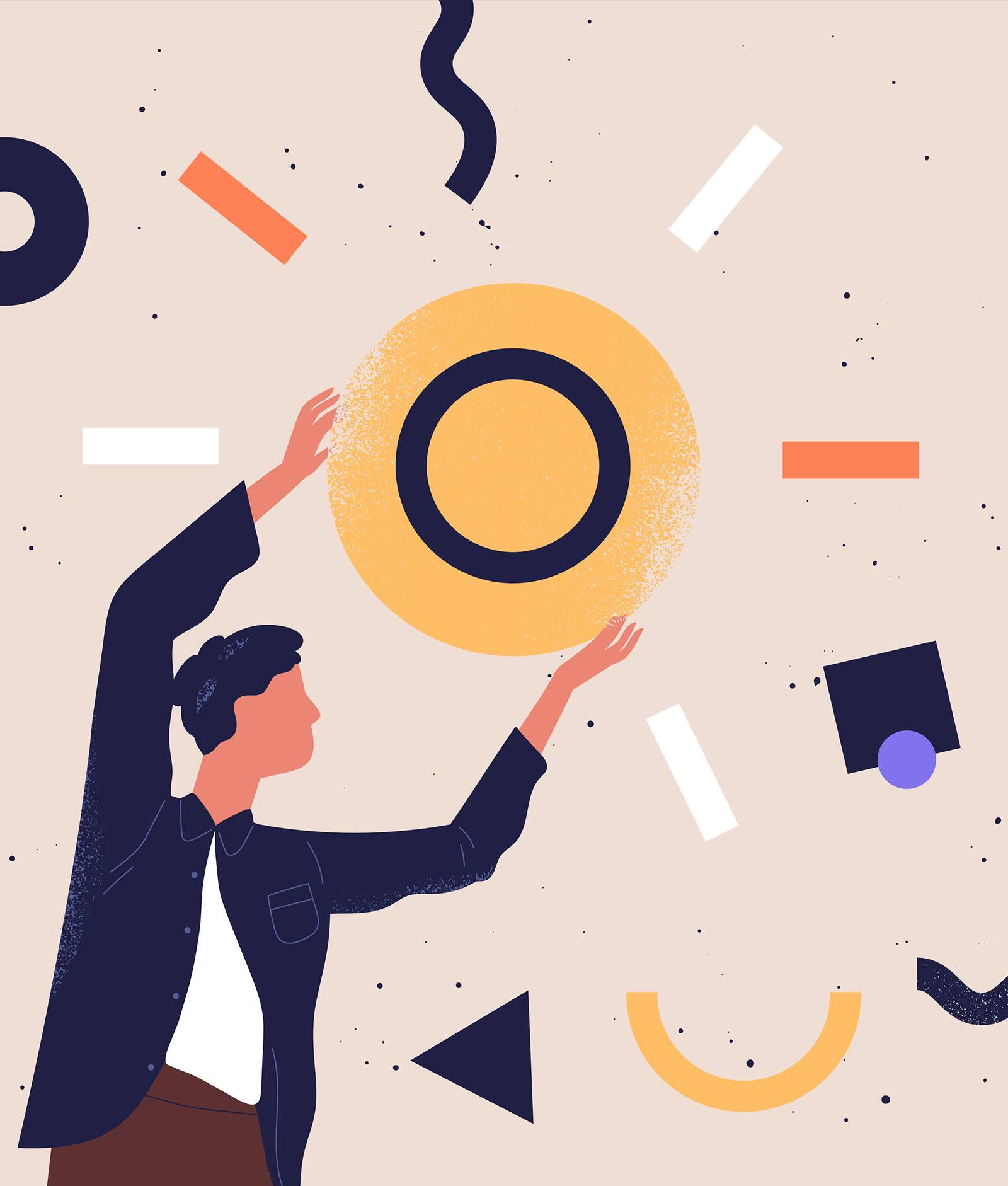
Turneky Solutions Development
Digitise your business infrastructure with scalable web applications that improves key facets of your business, from automation to collaboration. Leverage our expertise to build an enterprise software solutions that solves a particular business objective
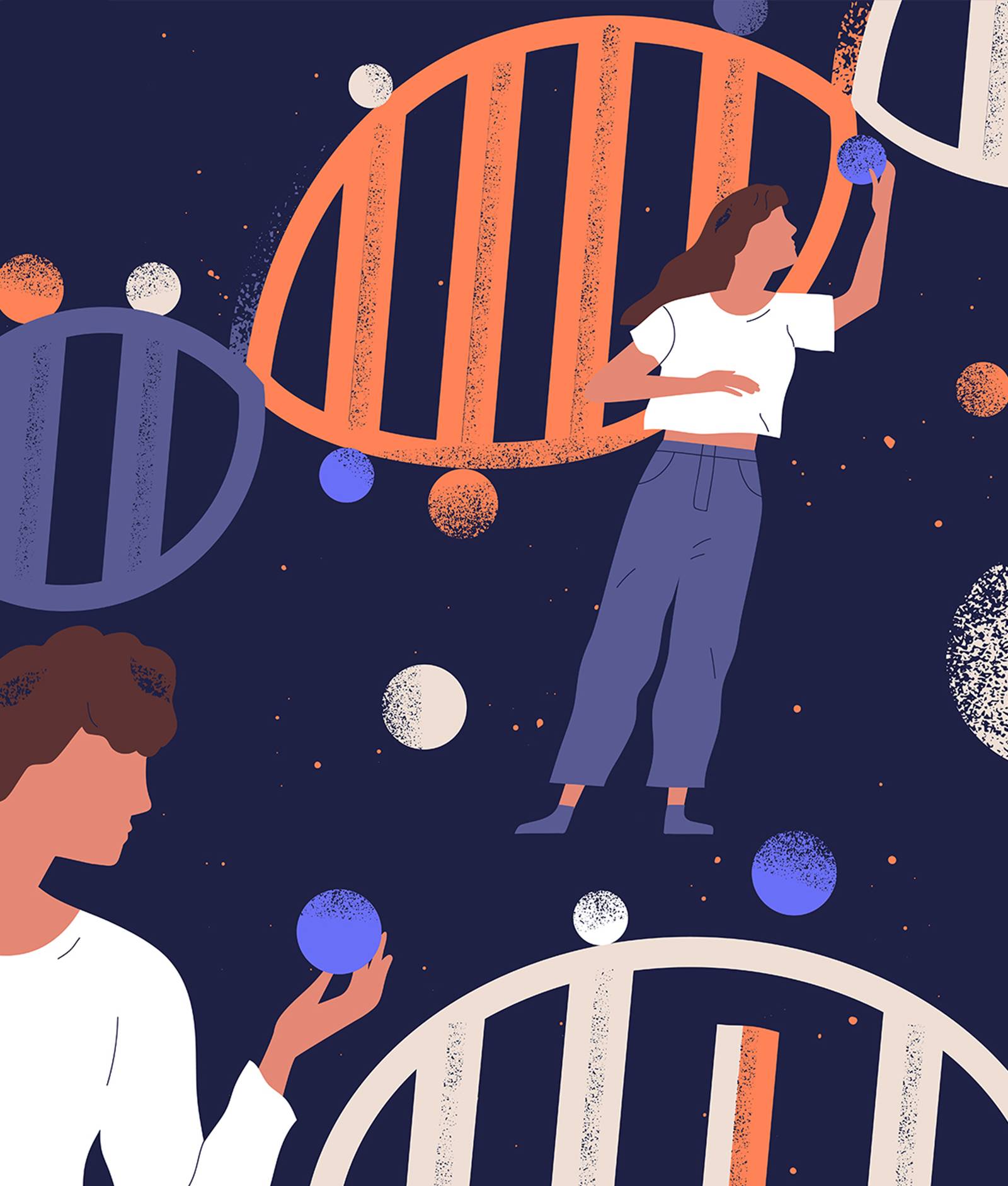
Software Product Development
Delivering software solutions to both established world-brands and innovative start-ups. Our team of experts have extensive experience in providing customized software solutions for businesses of all sizes, regardless of their level of complexity.
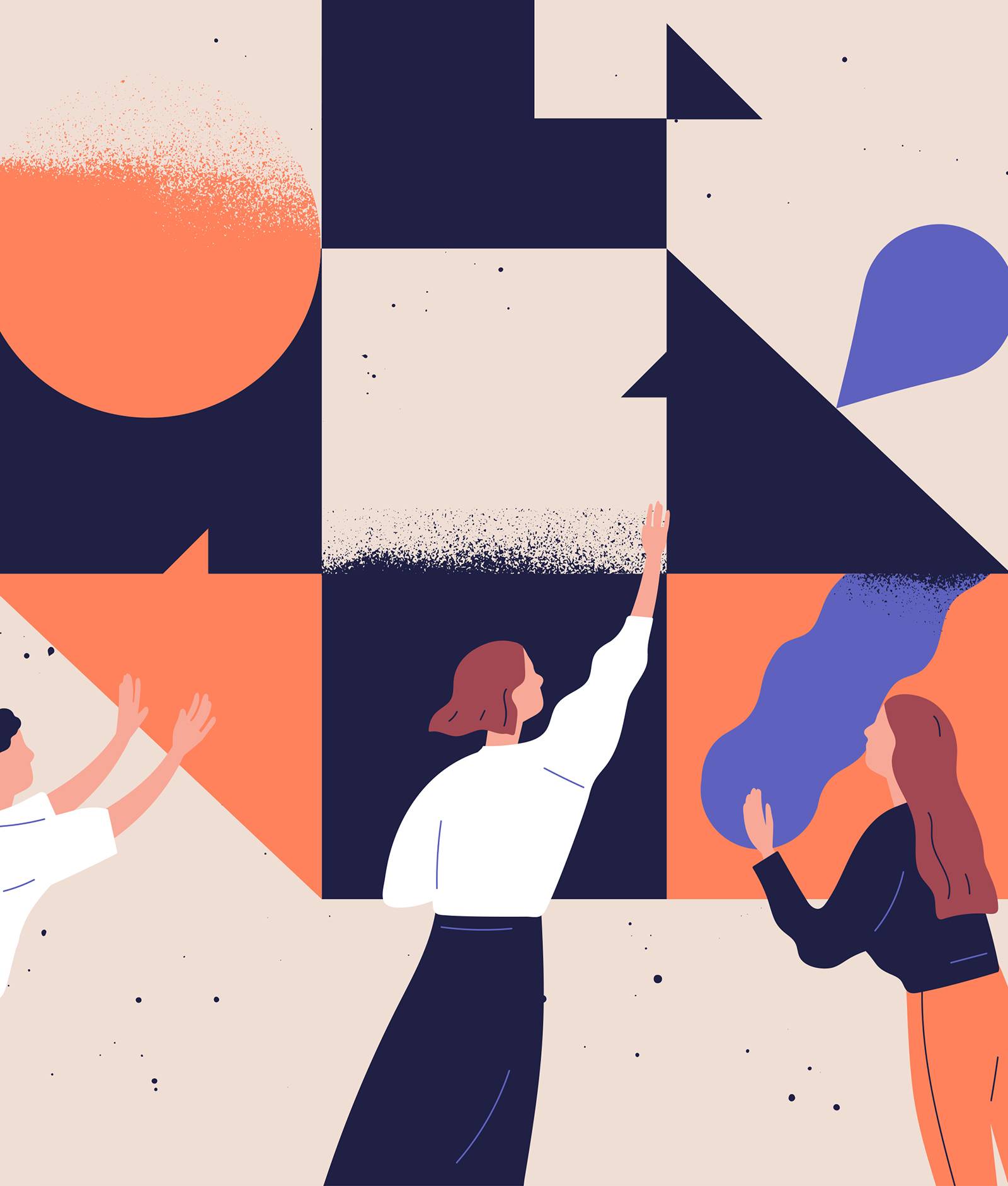
Re-engineering and Enhancement
Outdated enterprise applications often cause employees to spend more time working around limitations. We can perform an in-depth technical analysis of legacy solutions, re-engineer and improve it with the latest tools and technologies
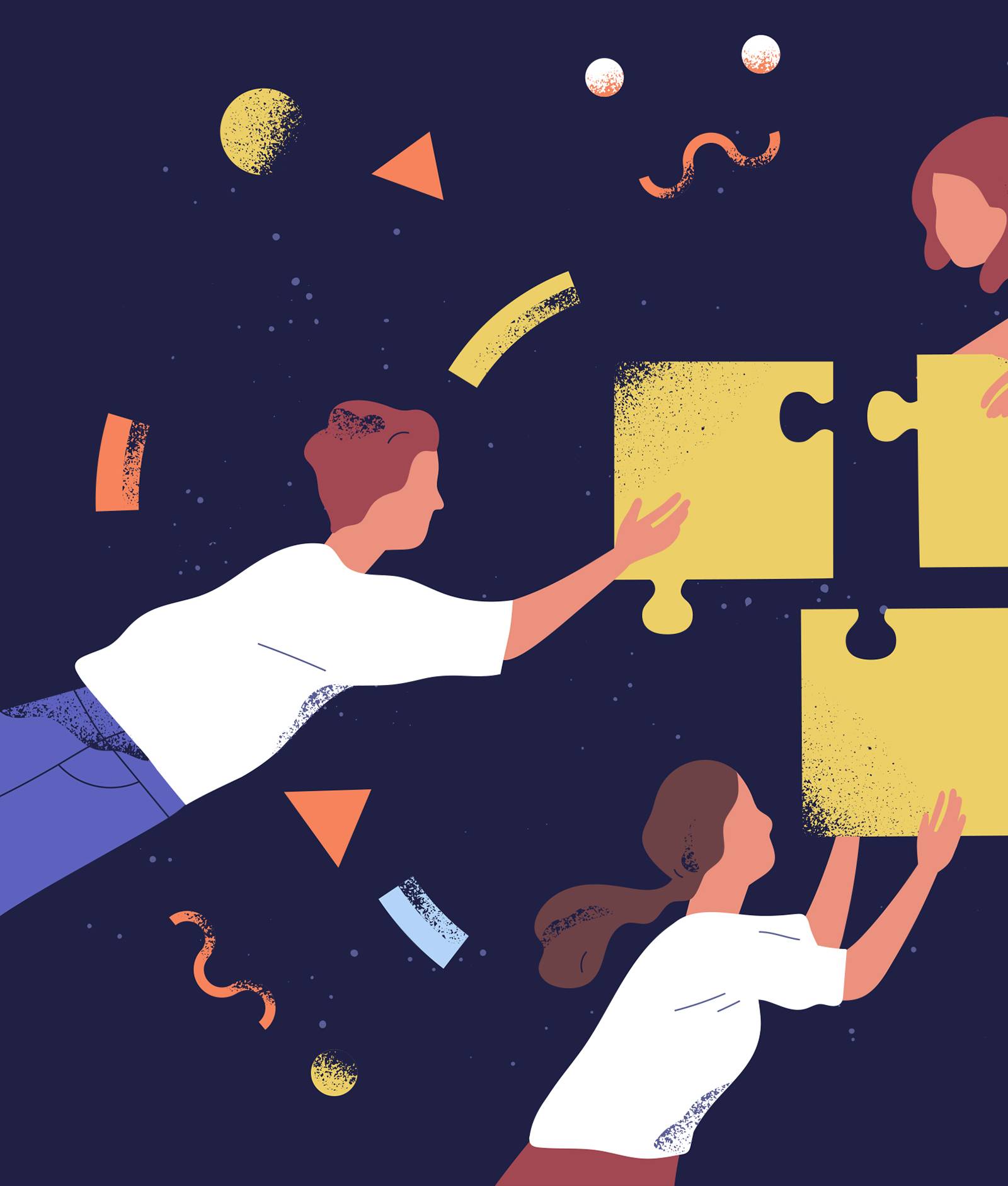
Business Analytics
Enhance your business processes, get valuable insights, and take well-grounded data-driven decisions with our big data solutions delivered to time and quality.
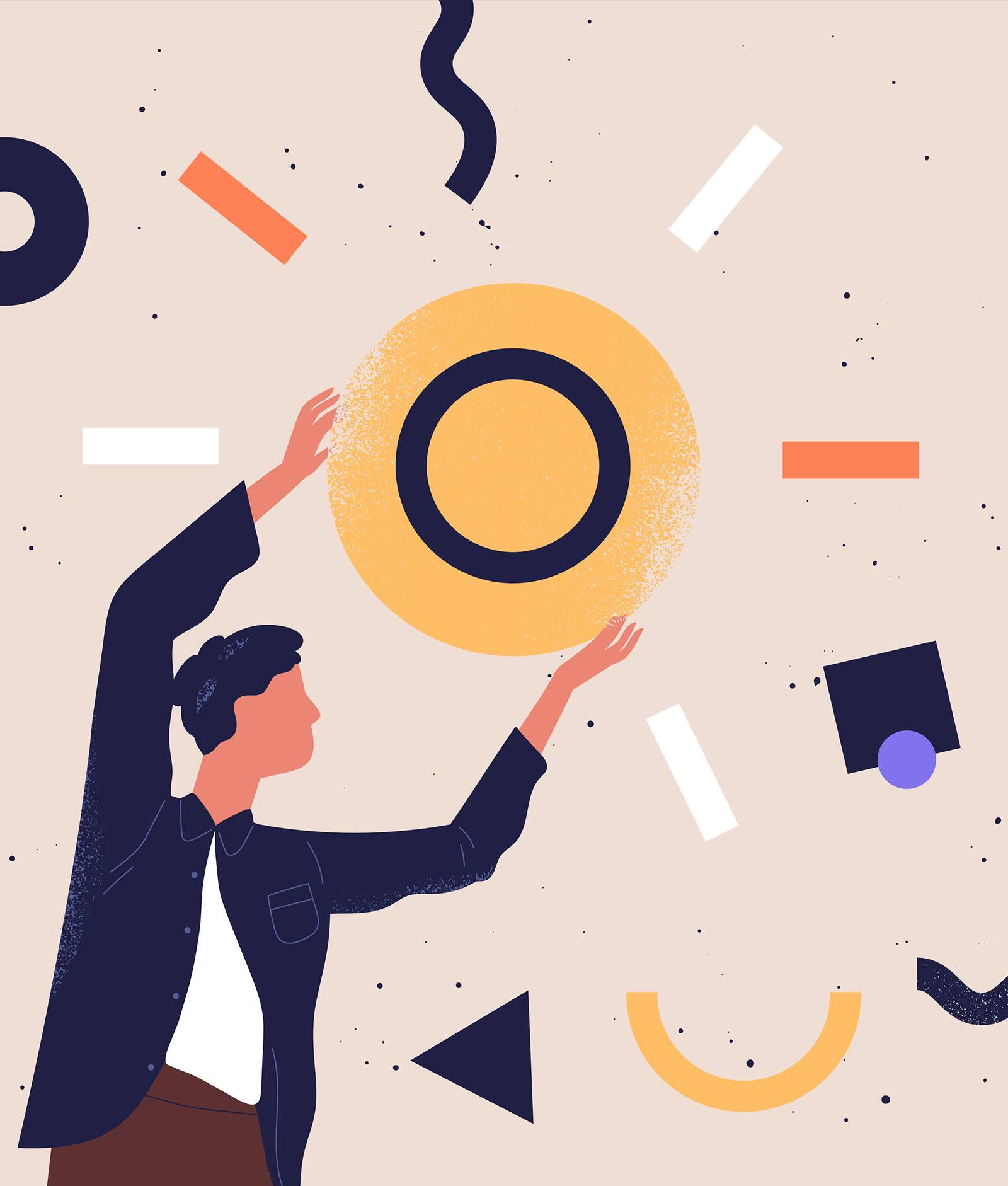
Software Integration
Improve your software applications infrastructure with well-built microservices, reliable API, and data integration
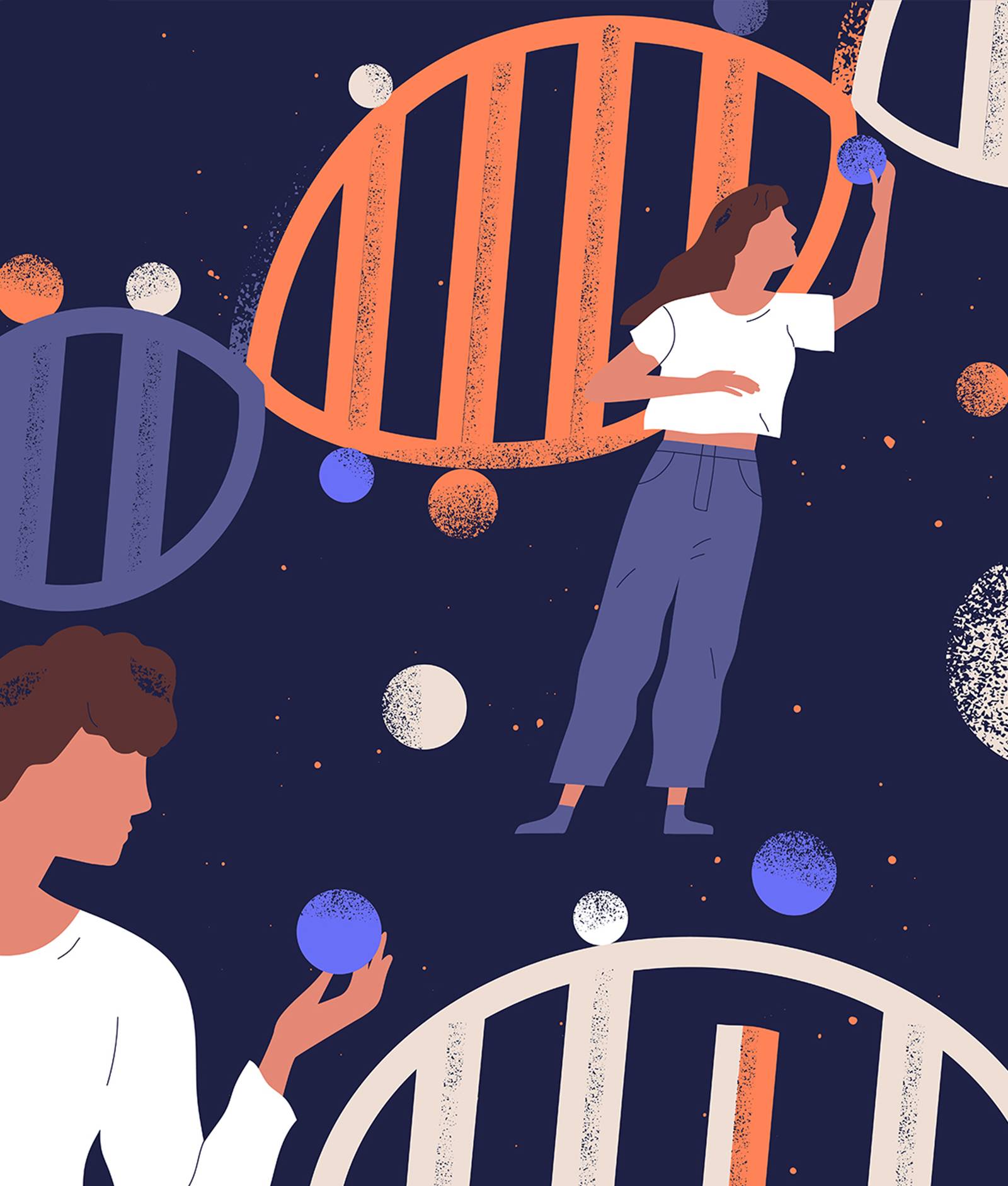
DevOps as a Service
Accelerate time-to-market, increase agility, and streamline software deployment, support, and maintenance with a reliable DevOps service provider by your side.
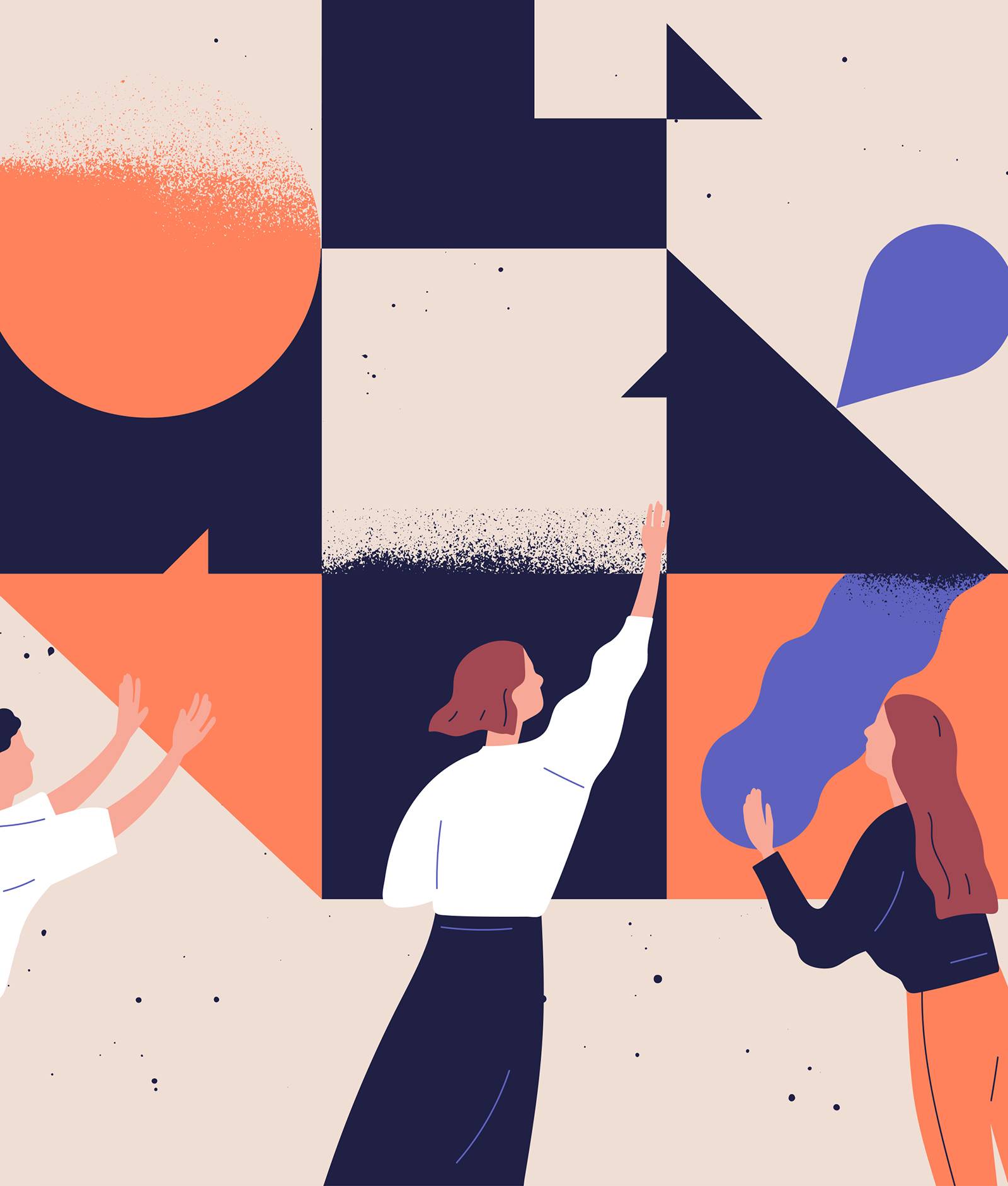
Software Testing
We perform both manual and automated testing to provide you with the data, metrics and KPIs essential for deep understanding of your current product state and evaluating your process efficiency.
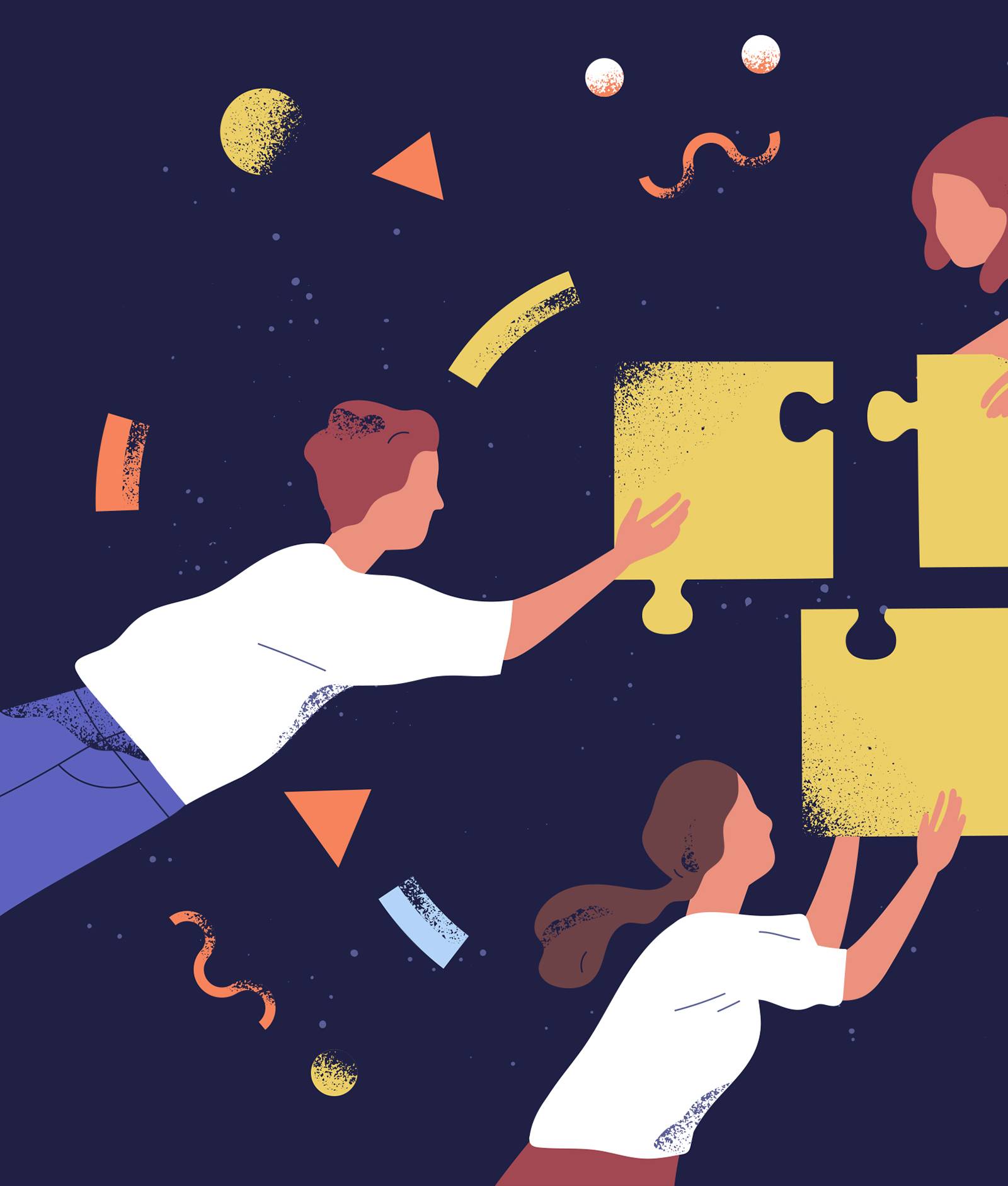
Mobile Apps Development
We don't restrict ourselves with development, we also support, maintain the apps and help our customers to meet changing requirements of the business with ticketing platform and resolution for issue as per SLA
Delivering business success
We develop smart and intuitive solutions tailored to the needs of our clients. With experienced professionals and agile methodologies, we efficiently overcome the expectations of customer business goals. Ready to Improve your Business Performance?
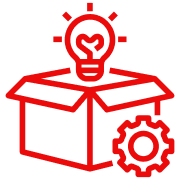
Product and Services Innovation
With a product development process, Montbleu can design, build and launch digital products with impact and scale.
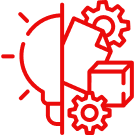
Deep Design Expertise
Montbleu combines expertise in human-centered design, business strategy and financial analytics to drive growth.
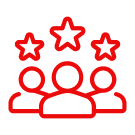
Transform Customer Experience
Leverage human-centered design to improve CX by optimizing customer interaction and removing friction.
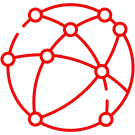
Go To Market Faster
Unlock extra value with custom-made product design services and new business models with closer user connection.
Automotive Embedded Services
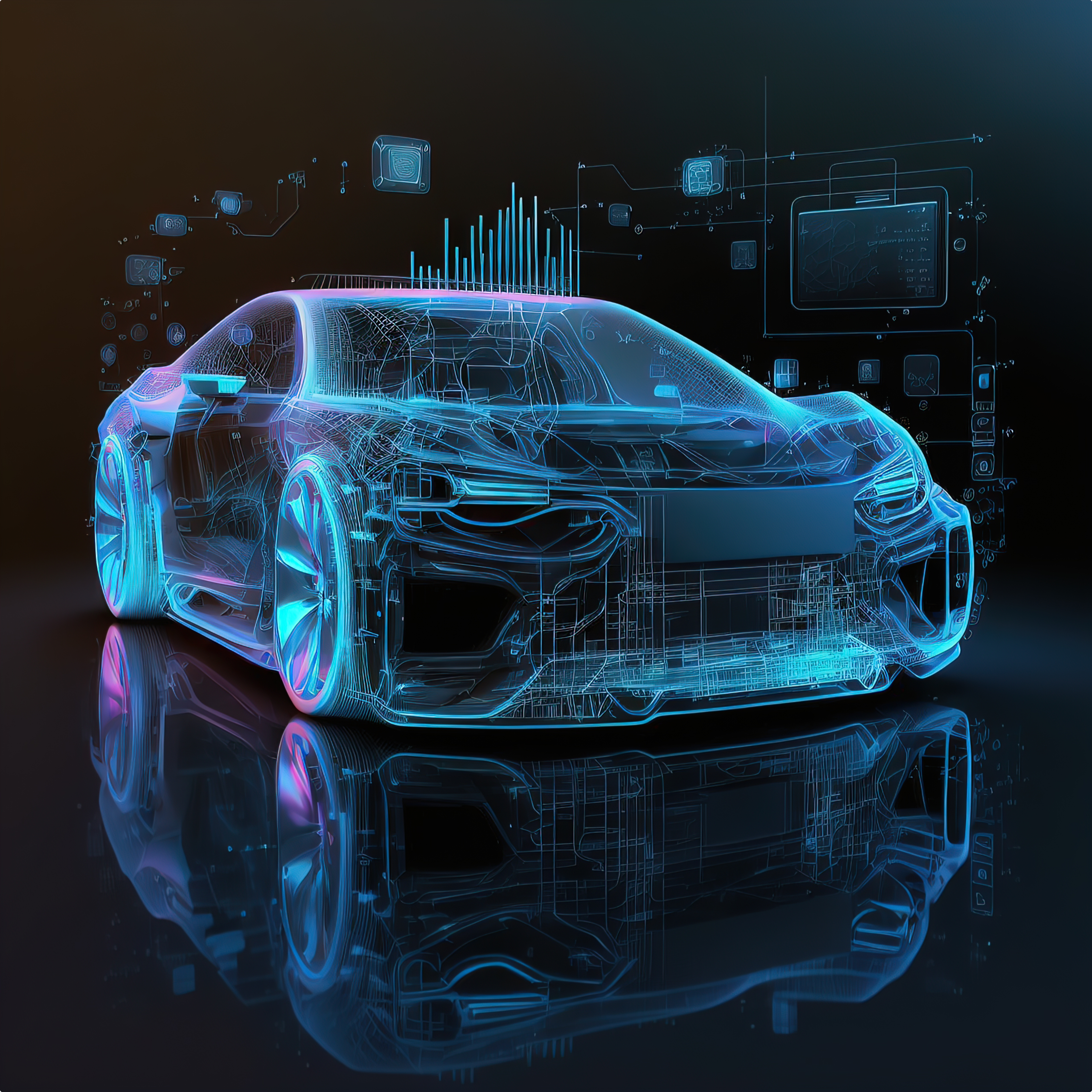
User Experience Engineering Services
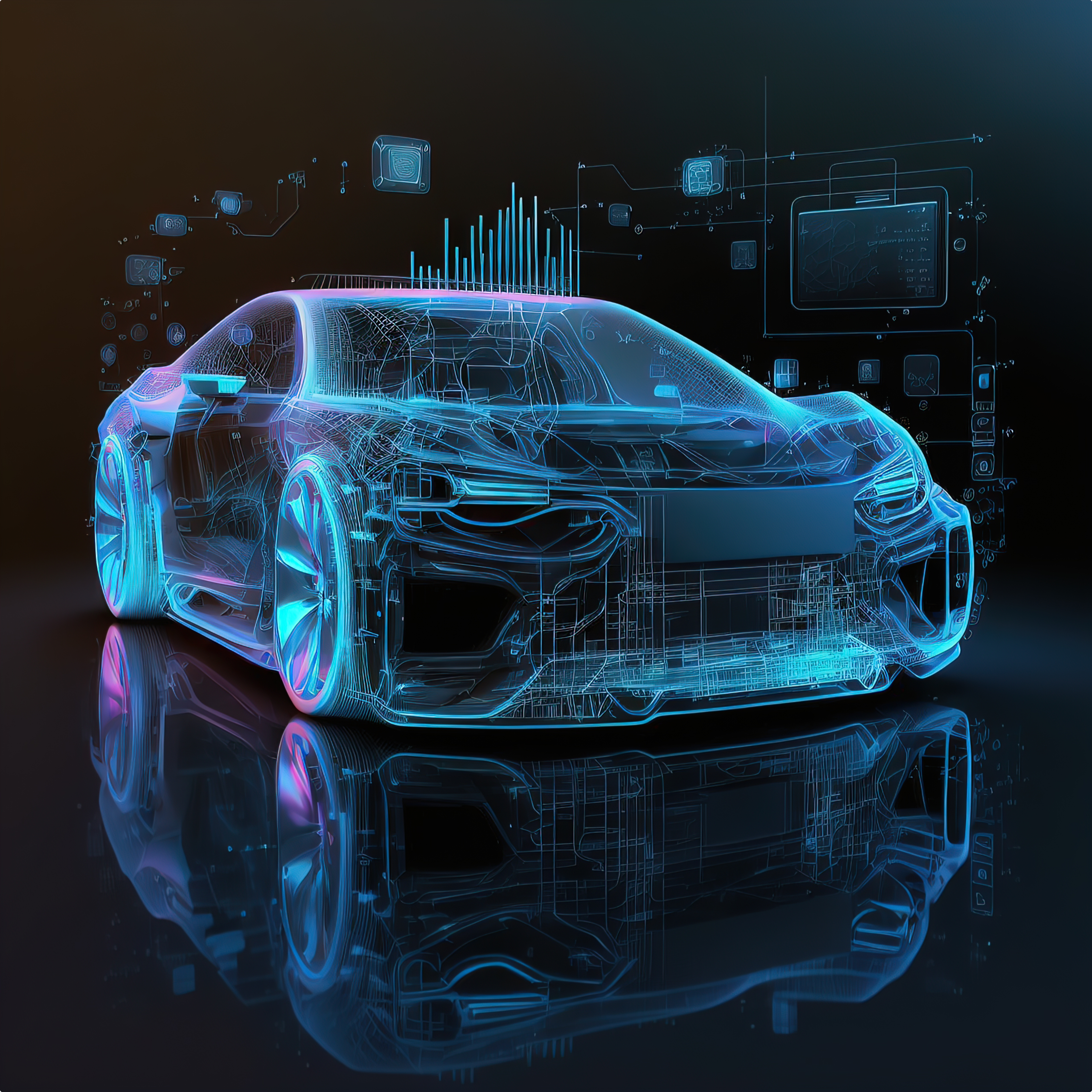
ADAS Engineering Services
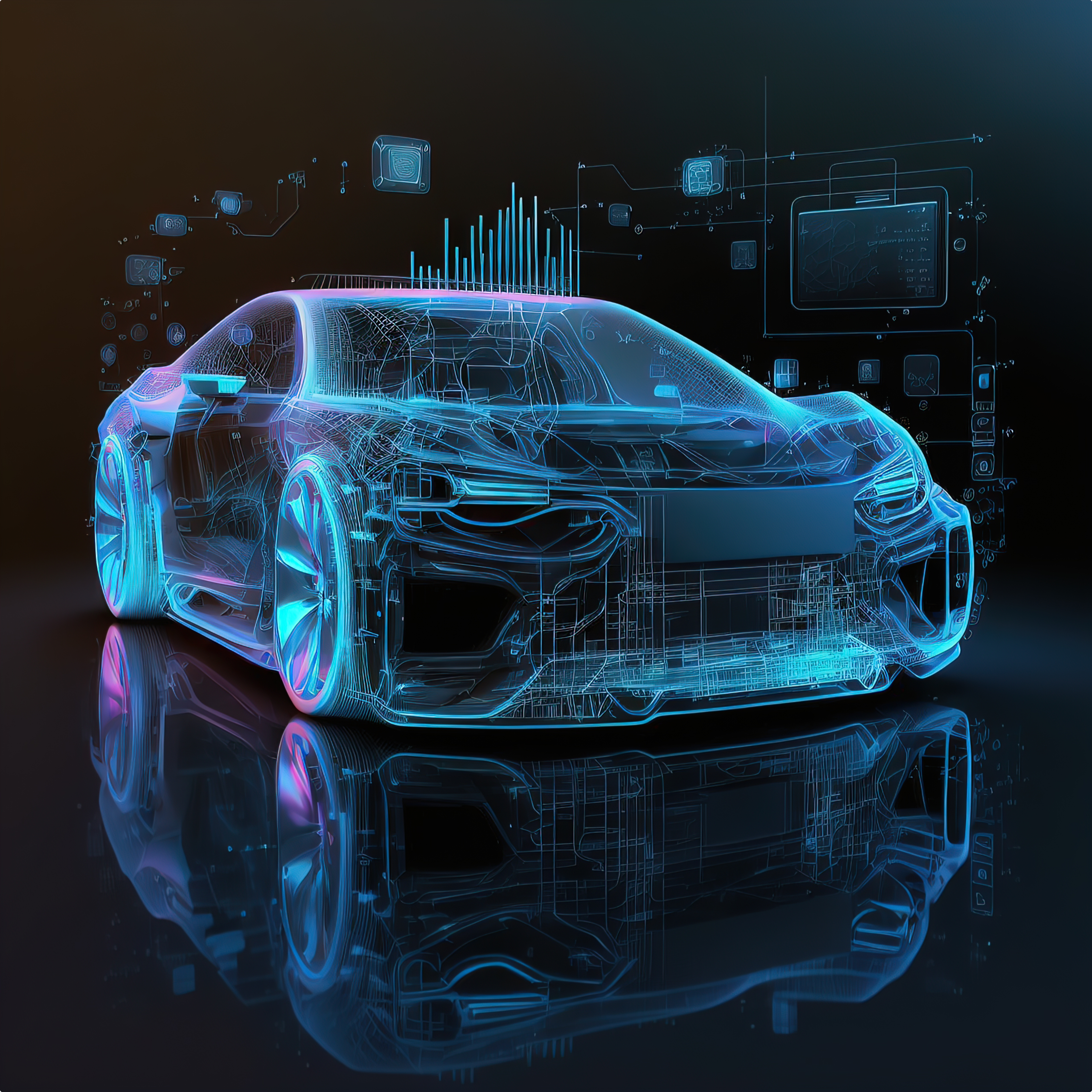
Software Testing & Test Automation Services
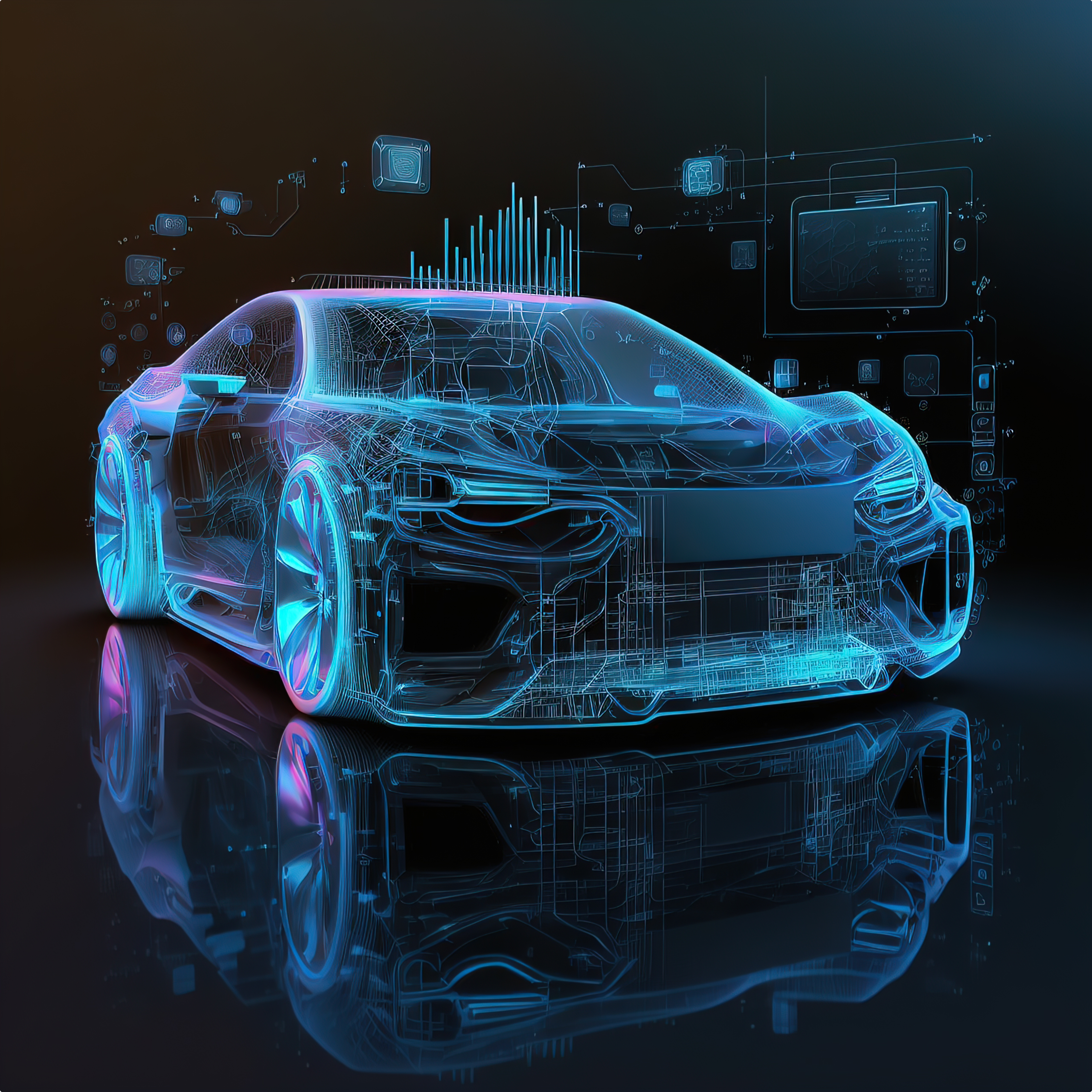
ECU Software Engineering Services
Your full-service technology partner that provides solution design and delivery excellence
Accelerating the transformation to software – defined vehicles
Competence
Services
User Experience Engineering Services
Services
ADAS Engineering Services
Services
Software Testing & Test Automation Services
Services
ECU Software Engineering Services
Automotive E/E Domain Capabilities
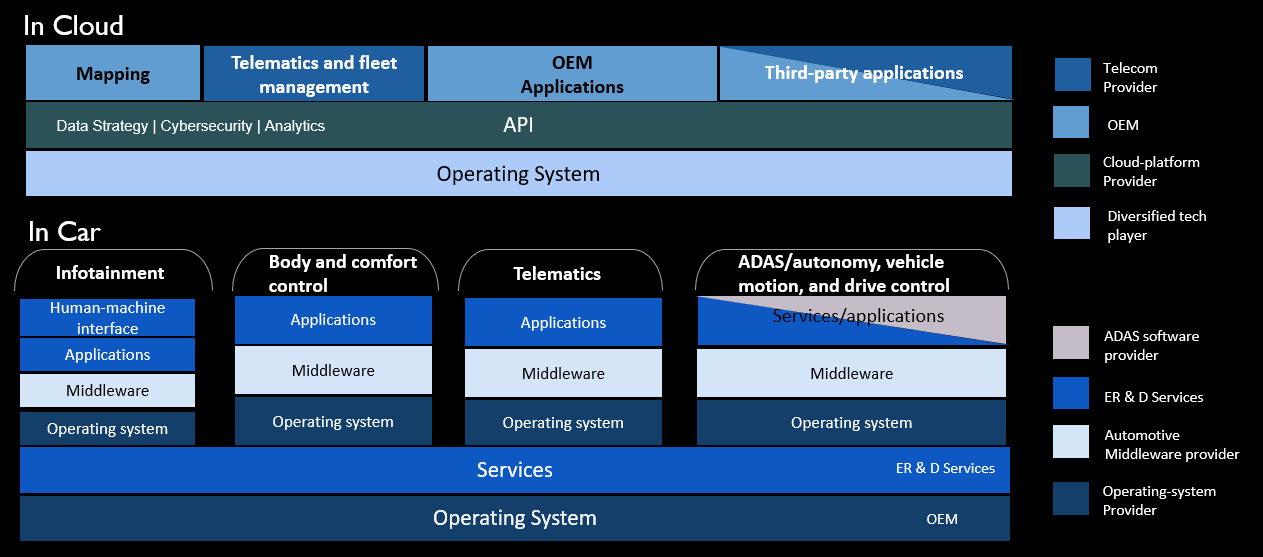
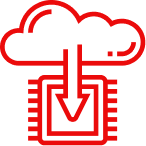
Firmware, Middleware
System Architecture and Partitioning, MCU Firmware, HAL, Protocol Stack Development, Power Management, OTA Firmware upgrades.
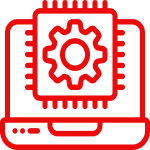
Device Drivers
Kernel Device Drivers such as: Bus Drivers, Wifi Drivers, Audio & video Drivers, Camera Sensor Drivers, Display Drivers, MIC Drivers.
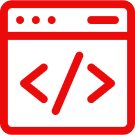
Bootloader Development
Bootloader Development / Porting and hardening on different architecture platforms, Boot time optimization, Customized API Development.

OS Porting and Customization
RTOS Porting / Development: Linux, uCos, eCOS, System Android Porting Development, Optimal performance with low memory footprint.
Automotive Software Engineering Process
Quality management ISO 9001 - 2015, Automotive SPICE
Functional safety ISO 26262, IEC 61508
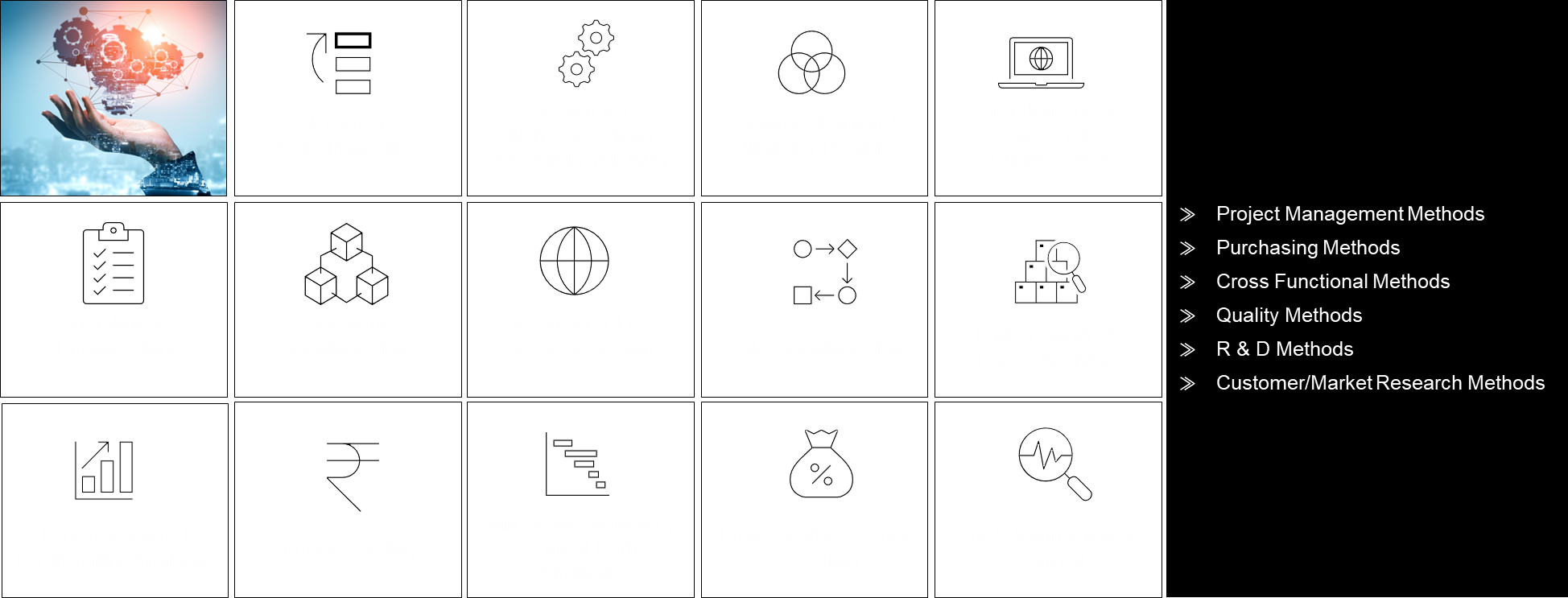
Engineering as a Service
GCC as a Service
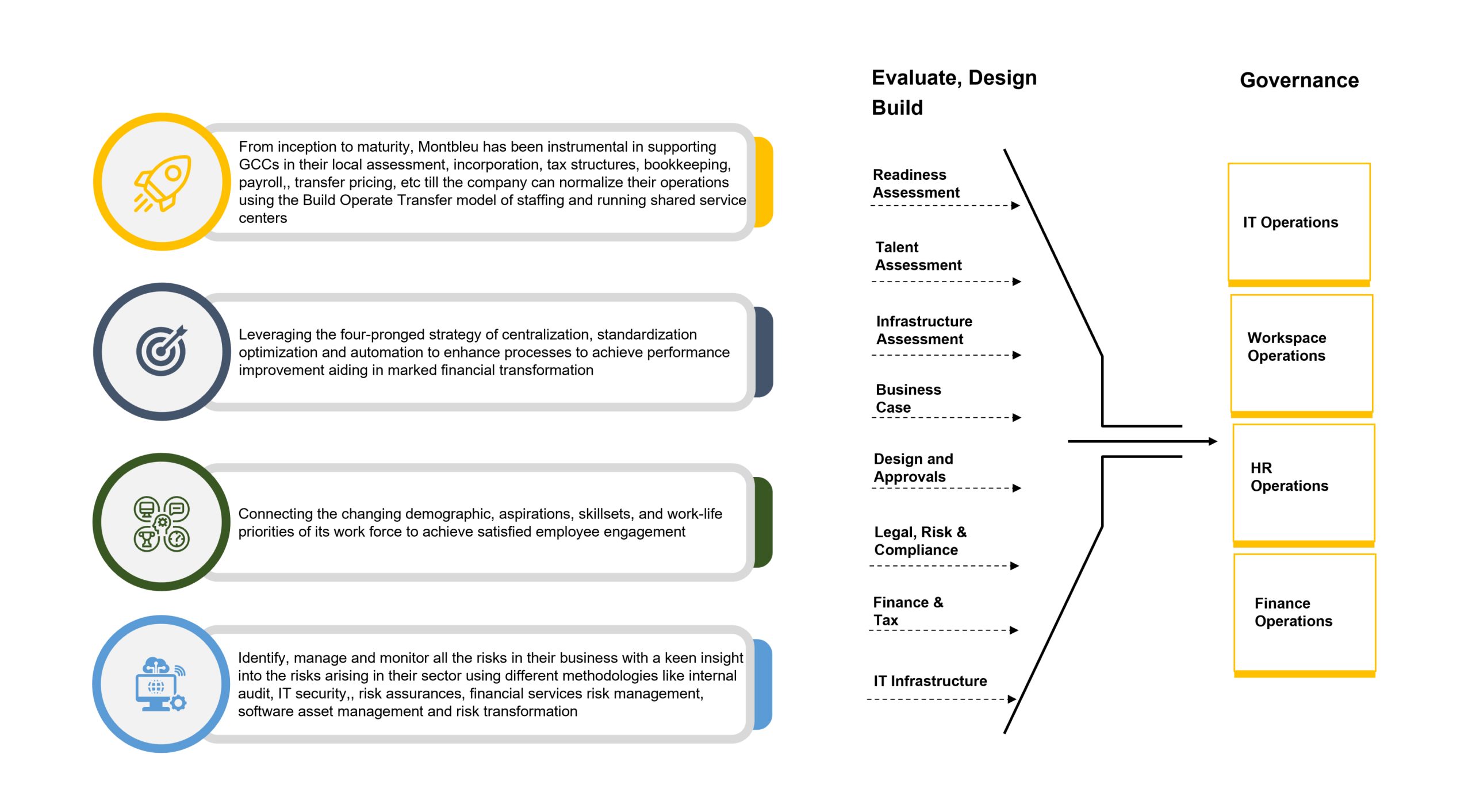